3-d Printing is much more than little trinkets that out kids make and give to us for Christmas, 3-d printing from a prototyping standpoint is power in your hands.
The advantage of 3-d printing is that it allows any design to be made, regardless if it actually can be made using conventional methods, such as CNC routing, die cast molding. The problem with CNC routing for example is that the line-of-site of the tool is all that can be machined. (We are talking about conventional 3-axis cncs, not 5 axis, 4th axis or even 6 axis machines – as that can machine in areas that 3 axis machines cannot…that for another article.)
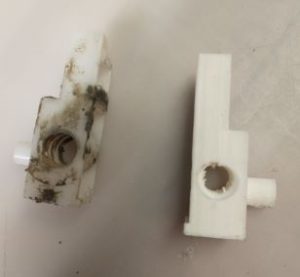
Screw Guide for cat little machine. The inside threads were stripped out on the original design, the 3-d printed part on the right (though mirrored here) made an extremely durable replacement part.
What this means is that a part typically cannot be machined if it has undercuts, or has a feature underneath that cannot be reached by a tool coming at it from one direction. 3-d Printing generally speaking dashes that mold. The part can be designed with undercuts, can be designed so that it is hollow, can be designed so that it has complicated shapes such as involute profiled gear teeth, helix shapes (such as a screw), integrated parts that hinge together, but could never be assembled in the first place, such as a loop chain.
At Prototype Industries we do offer 3-d printing services, but our emphasis on 3-d printing in the prototype process goes way beyond the first prototype. Generally we may make a first prototype using 3-d printing, but we typically use the 3-d printer for making mold forms and fixtures. This cuts out enormous amounts of Machine time and labor to make a simple fixture or even a die set.
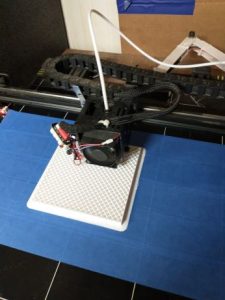
A larger part 5 x 6 x 3.5 tall (when it is finished) is being printed on our large printer.
Our use of the 3-d printer widely varies, and for that reason we have several different versions. We have smaller unit to just get the job done quick. We have a larger unit to do large parts: 15 inches x 15 inches x 15 inches is possible with the printer that we have. Sometimes if the part is even bigger, it can be broken up into smaller sections and then glued together later.
An example of our use for the 3-d printer is to develop mold dies for foundry work. Patterns can be developed that are very durable, however in our processes here at Prototype Industries, we use a different process that does not put strain on the 3-d printed die, but allows multiple die sets to be made off of it.
We routinely produce these large wheels for a go kart customer that supplies Model T Go kart wheels to the McDonough, Crue Cut and Mini Kar market. These wheels are so duplicate-able that they locate on the CNC fixture without variance. The parts have remarkable consistency and show the dimensional accuracy of 3 d printing and the resultant patterns.
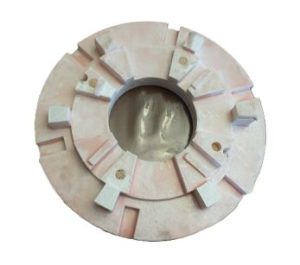
3-D Printed CNC Fixture for machining Model T Go- kart Wheels
The concept of wheel holding fixture was develop off of models, tested as a concept with a wheel that was cast. The fixture then was reprinted with aluminum shrink added to it (because the part will shrink down after it is cast), and the resultant part was open faced cast. (The part was also designed to be optimized for open face casting to minimize point shrinkage or “suck in voids.”)
To demonstrate the accuracy of the 3d print, a fixture pattern was develop and used as holding fixture for the wheel in the CNC machine. The resultant casting was brought to a machine shop and all that had to be done was minor back facing to true up the parallel to the machine plane, and minor if any trimming on the mating surfaces to hold the wheel in place.
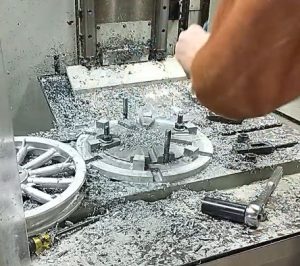
Wheel Holding Fixture for CNC milling of the Model T Go kart Wheels
3D Printing is used extensively with fixturing and is bolstered in strength by backfilling the actual part with Urethane. This makes the fixture flexible enough to be used in repeated fixture, but also durable, like aluminum or steel, to hold the part for tight tolerances.
The following part is held in place on the CNC plate surface by conventional hold down hardware. The location is simple with a center hole used during alignment set up. The part being machined, the Snake Guide Block, is held in place with a simple 3d printed urethane filled clamp. These fixtures last in the thousands of part cycles and can handle the adverse conditions, most notably that they don’t rust.
This is another example of a 3d Printed Urethane filled fixture being used for a round part that require the ends to be finished off. The down side to open face molding, is that one end is pretty rough. The surface tension of the urethane climbs up the mold surface and makes the filled face uneven. Having a closed face mold makes casting urethane more difficult as voids, bubbles are hard to get out of the casting, not without expensive vacuum assist equipment. The compromise is the simple open face mold, with secondary trimming operations. This is the most cost effect and actually timely solution.
To recap, Prototype Industries uses 3d printing for the following purposes
- Initial Prototype
- Mold Die Forms
- CNC or Lathe Fixtures