Urethane is an elasto-polymer that is made up of a two part mix that chemically bonds into a rubber like material. It has various degrees of hardness that are evaluated by durometer, at type of hardness measurement.
Urethanes are susceptible to petroleum based products so they should not be mixed, but they do have excellent properties similar to plastics.
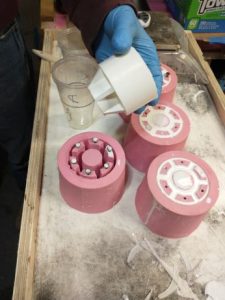
Demonstrating how a silicone rubber mold can make a complex part. This type of mold is called Open Face
The benefit of using urethanes is that they can be poured at room temperature into molds, unlike plastics and rubbers that require heat and pressure to be extruded into expensive steel tools or dies.
Urethanes have the bending and tensile strength similar to thermal plastics such as polyethylene, polypropylene, ABS, nylon and UHMWPE. Urethanes can come in many shades transparency clear to opaque.
When urethane bonds to metals or plastics the bond is aggressive, however it requires a rough surface finish for the best adhesion. It tends to bond to paints and sanded surface quite well. The bond is not chemical in nature but mechanical, and therefore can lose grip when it gets hot or increases in temperature.
Urethanes will bond well to similar urethanes as they will make a chemical bond with eachother, especially if the material is freshly poured.
There are different strengths in urethanes, typically the higher the strength, the longer the cure time, as the chemical reaction has to be very thorough. Also, the ultimate strength may be high, but the brittleness or shattering ability is greatly increased with the high strength urethanes.
The urethanes that are middle of the road, 2500 psi versions tend to be more bendy and will not shatter but elongate. Depending on your application you may want to contact us concerning the strength that you are looking for on your part and we can work that in.
Urethanes an be machined and drilled. They tend to chip if aggressively hit, so sharp tools are required for milling and lathing out parts. We routinely perform secondary operations that require pocketing out part, drilling four holes and then adding a chamfer on the top edges. This particular part is used in a Plumbers Snake Machine to keep the snake from eating up the entry path on the wind up area on the machine.
The time it takes to set urethanes varies from ten minutes to 20 minutes depending on the type chosen. For example a slow cure urethane is used in rotomolding applications as this allows the material to flow around the tool as it is rotated and then coat the inside of the part evenly.
Simple open face molds that don’t require long set times can be filled with a fast setting material that cures in 10 minutes. The material however will increase in temperature significantly, to the point of not being able to either touch the molds or the parts as they come out of the molds.
Urethanes are an excellent and simple choice for rapid prototyping or for simple solutions to simple problems such as replacement gearing or high wear parts. The benefit of urethanes is that it suites low production run orders. We typically take orders for 100 pieces to 300 pieces. The most a tool will take is around 75 parts before the urethane itself starts to attack the silicone rubber molds.