Aluminum and Brass casting is where molten aluminum or brass are poured into molds and then the molten material solidifies and shrinks to the final shape.
The aluminum we cast with is an alloy of A356 that is used in casting cylinder hears for cars. The advantage of this material is its forgiving casting characteristics and its durability, especially when machining.
There are several ways that molds are designed. The simplest method is a sand cast mold, the more rapid method is the aluminum or steel mold system. There is also plaster casting which makes very fine detail parts but requires an exstensive burn out time to get the moisture out of the plaster.
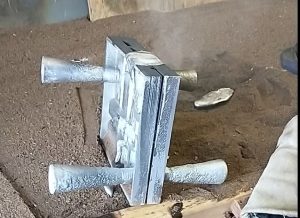
Solid Mold made out of aluminum to cast aluminum by gravity casting.
Note: The aluminum or steel mold system is similar to die casting but it is called solid mold casting, because the molds are gravity fed, not force fed as in die casting. Die casting equipment has a piston immersed in molten aluminum that shoves the material into the mold. This equipment is specialized and requires high part volume runs to justify even warming up the machine.
The most cost effective method for making small batch runs of part is the sand cast method. We do not do green sand molding, where the pattern is compacted in wettish clayee sand and then the pattern removed, this method is way too touchy and time consuming. We use a proprietary method that has a 95% success rate in part quality.
If making one off’s is really all that is required there is lost foam casting. This is where the part itself is machined out of foam, sprues and risers are glued to the part. After that a refractory material is coated onto the part and then allowed to dry. The part is then immersed in sand and vibrated to compact the sand around the foam part. When this is complete the molten aluminum (or even cast steel, brass, or iron) can be poured into the sprue. The immediate action is the foam vaporizing and burning away. The refractory material has enough strength to it to keep the sand from collapsing around the sudden void as the foam disappears.
The resulting casting is the part in high detail. Whatever the foam looked like, that is what the surface of the part will look like. For more information about lost foam go to this page.
Aluminum and Brass casting are two viable options for making durable parts. Typically an aluminum mold system can be used to mold a brass part, but voids and shrinkage are inevitable when doing this. Some parts can get away with the extra shrinkage, however it is recommended that the decision to make either aluminum or brass be made early in the cycle so as to get the tooling right.
Brass (density .313 lb/in^3) is notably heavier than aluminum exceeding its weight by nearly 3.13 times (Al Density .100 lb/in^3). It is also heavier than steel, which is .283 lb/in^3
The advantage of brass is its resistance to corrosion and its ductility. The ductility makes it suitable for load applications and quite frequently is used in worm gear boxes. It is also easily machined. The corrosion aspect comes in to play for high corrosion environments such as salt and water immersion. Frequently brass propellers are used on boats for this very reason. The corrosion resistance also makes it ideal for prototypes, especially for ornamental prototypes. The shine of brass is like to that of gold. It is quite impressive.