Tooling is a way to make parts in multiple form without having to hand carve each piece by hand.
For our prototyping or short production run jobs tooling is the critical element to get the job done efficiently.
For our processes, we use the following tooling methods:
- Silicone Rubber Tooling
- Sand Mold Tooling
- Plaster Mold Tooling
- Permanent Solid Tooling
Silicone Rubber Tooling
Silicone rubber tooling is the simplest and quickest form of tooling that we use. The concept is to cover the part that is going to be duplicated with liquid silicone rubber. This a liquid form penetrates in every crevice on the part, so that when it becomes cured as a rubber form it has the part details imparted onto the surfaces of the rubber that contacted the part.
The silicone rubber is then prepped so that the part can be extracted. On an open face mold, the rubber is simple pulled off of the part and one end of the resultant rubber cavity is left open.
On fully enclosed molds, such as the rotational molds, the cavity is split in half. Alignment of the molds can be tricky so there are various methods to make the molds line up perfectly every time. Some of the tricks involve just a simple ragged edge cut with a razor blade, but the more duplicate-able methods involves thoughtful placement of pegs or protrusions that will locate the mold accurately every time the mold halves are brought together.
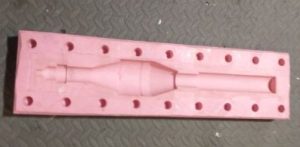
Rotational Mold, with alignment peg holes. Tool is expired as there are parts of the tool missing
Silicone rubber tooling is used primarily for urethane based parts, unfortunately only about 75 parts can come off of the tool, as the urethane degrades the silicone. At the end of the life of the tool, the surface of the tool will start to stick to the part. Frequently the last parts will have chunks of silicone rubber stuck to the surface, obviously indicating the end of the tool!
Not all urethanes degrade the silicone tools though. As a rule of thumb, the quicker the urethane sets, the faster the molds degrade. Also the faster a urethane sets, the hotter in curing the urethane gets. It is not uncommon for a part to be so hot that it cannot be handled after it has cured. This heat actually is the enemy of tooling, so taking a break for example to cool the tooling down is sometimes employed.
Sand Mold Tooling
Sand Mold Tooling is designed for metal casting, and is the step that is needed if metal parts are desired. The tooling is suitable for making castings for aluminum, brass, steel, zinc and cast iron.
Sand Mold Tooling is an odd way of describing tooling, however that is what it is. Tooling is made to form the sand. You may be thinking, oh a pattern. You could say we are making patterns, but these patterns a made out of rubber, whereas patterns in the foundry world are made out of wood or hard plastic, so that green wet foundry sand (or even Petrobond) is packed onto the pattern, and then you cross your fingers and hope the pattern un-sticks from the sand. Inevitably chunks of the sand fall away and ruin the resultant mold.
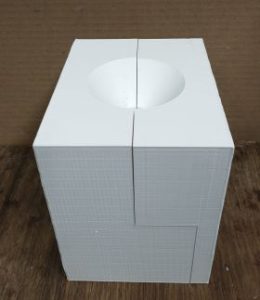
Initial 3d Printed Mold Design.
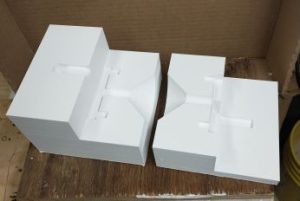
3D Printed Mold Halves separated. These mold halves will later be encased in rubber to form a sand mold.
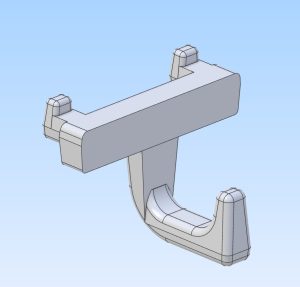
Intended part from the molds
Sand Mold Tooling is developed from the model stage, then the resultant tooling design is encased in silicone rubber. Currently the technology we use is the end filling method, as the sand itself is hard to pack into enclosed spaces.
Plaster Mold Tooling
The advantage of using silicone rubber tooling is that the same tooling used for making sand molds can be used to make plaster molds also. The disadvantage of using plaster tooling is that it takes days to dry out the plaster. This drying out is expensive driving the cost of parts way high. Often customers will just opt for the sand
molding as the only real benefit of plaster casting is the excellent surface finish attained by the plaster molds. Also, vents need to be made in the plaster tooling otherwise gas gaps voids will show up on the surface of the part. Careful attention to venting needs to be made, and sometimes this can be a trial an error method before good parts are attained.
Permanent Solid Tooling
Solid tooling is the long term investment for dependable multiple part orders. The materials to be cast range from molten aluminum to urethanes. Brass can be cast using solid tooling however the tool itself requires cooling to keep the tool from degrading. Urethanes can be cast in solid tooling as well, but require ample draft and thoughtful placement of ejector pins to evenly extract the part from the mold.
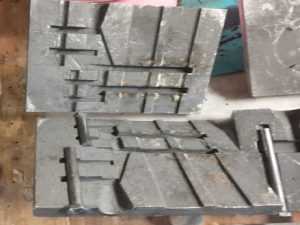
Permanent Solid Tooling. This tool makes two parts at one time. It also has core pins for each part. Not shown are other cores for the slots.
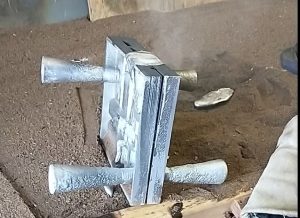
Tool filled with molten aluminum
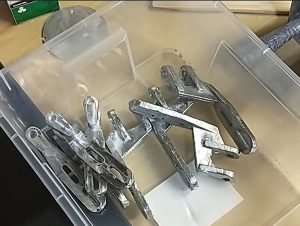
Resultant parts
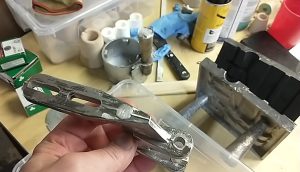
Up close detail on part
The solid tooling that is used by Prototype Industries is typically relegated for casting aluminum parts. As with any metal die, draft has to be designed into the part so that the part will come off of the tool when it is finished being cast. We have great success with solid tooling if multiple quantities are required.
The cost of solid tooling is substantially higher that that of sand mold tooling, however the part cost may offset the overall tooling cost. The cycle times for solid tooling is in the minutes, where as with the sand tooling the time required to make and prepare the parts for pouring is around 5 times that of solid tooling.
If multiple parts are required, tooling is generally required to keep the cost of each part in a manageable level.
The disadvantage of 3d printed parts and SLA parts is the strength factor and cost factor. With 3D printed parts the cost element comes into the time required to make multiple parts. It is cheaper to use Urethane castings for multiple parts that to 3d print the parts.