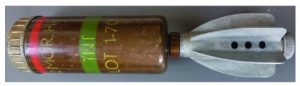
Mark 7 British Rocket Mortar
One of our clients works with re-eanactors and collectors by providing them with authentic war memorabilia. We have provided them with various types of movie props such as German Rocket propelled grenade props, or even clay-more mines.
These props have been used in movies provide the realism that many require for good story telling.
Recently, we have been requested to develop a Mark 7 mortar. A mortar is a type of munition that is dropped into a reinforced barrel that is pointed at an angle into the air. The mortar when dropped into the barrel has a charge in the bottom that goes off creating an explosion that fires the mortar round way up in the air. We all have heard the phrase “incoming!” and that is because mortar rounds are coming out of the sky as they have been fired from these mortar tubes.
This particular mortar is a collectors item and is not readily found for collection. So we were tasked with making a realistic facsimile out of aluminum. This will give it the metallic feel of a mortar round. Additionally the prop can be handled heavily without fear of it breaking.
The Recreation Challenge
Casting a part typically requires a simple two part mold, where the parts usually the same profile, so only really one side is required. For example on our large wheels only one mold half is made and the mold is essentially filled twice to make a wheel mold assembly.
On this assembly however, there are 11 pieces required to make the whole assembly in one shot
1. Six Fin Molds
2. Two Body Molds
3. One Core section
4. Two Mold halves for the cap
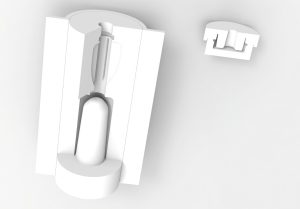
Mold sections for the mortar. 11 pieces required for one assembly
The tricky part is actually making the molds for the tail. Problem with sand molds is that one side of the mold needs to be filled. Secondly, the filling of the mold has to occur so that there are no undercuts.
This mold cannot be done with sand easily. To fill the rounded sections of the mold, the axial area needs to be feed with sand, then the whole mold needs to be capped off to make it round. This is nigh to impossible with rubberized molds that are used in simple processes. Getting a consistent rounded surface is not possible.
However, making the mold parts solid, is actually not so difficult, as the parts are made out of aluminum and just require several hours of machine time to develop them. The trick is to use a fourth axis to get the full 360 degree geometry needed for the profile.
There are several ways to make the tooling solid: machine or 3d print.
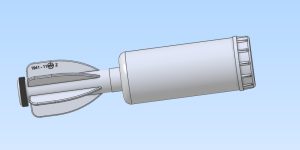
3-D Model of the Assembly Prior to Casting
In this case the tooling is going to be liquid (sla) 3d print developed. The individual molds will be developed making a mold for a mold. That sounds funny to say it that way, but what will be done is that end goal is to make a Mold. So a mold must be made, to make the mold. A mold must be made first for the rubber mold. Then the rubber mold will be used to make the resulting either sand mold, or plaster mold. The aluminum will be cast into the resulting sand /plaster mold and out will come the final “alumium die-cast” mold.
Sounds like we went around the block and back, but that is what tool and die makers do all the time. As I tell my clients, you have to learn to think backwards. Keeping track of the models and what they are for the part can be a challenge. There can be at least 3 different models that are required to make the final tools, or molds.
As has been discussed in other articles, getting the prototypes into production, or repeatable parts is best accomplished by die-casting tooling.
There are processes that can get some pretty good surface finishes using sand molding techniques, however, those methods do require that either steel and aluminum be cut to get “non-deflective molds.”
With the processes that we use in our prototype processes we can attain fairly consistent part sizes and consistencies using sand molds, but the “deflection of the molds” can cause part variance. To get around that, urethane molds for packing sand into, can be developed however generous draft is required, along with ejector pins. We do develop these style sand molds, however, in the long run die casting appears to be the most cost effective from a short run and quickness stand point.
For more information, we can discuss the various rapid prototype options to you personally. Go to our contact page for your inquiries.
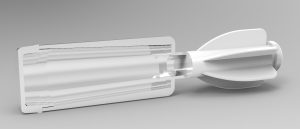
Cross section of part to be cast.