CNC Machining is an abbreviation for Computer Numeric Control Machining. The significance of the CNC machining is to show that we rely on the accuracy of computers versus manual machining. Also, the automatic nature of the CNC machine makes it a hand off operation where the work can be done, while being unattended. This can be a significant cost savings especially when manual labor is an issue.
CNC machining for Prototype Industries is significant in our work, in that precise location of secondary operations can be attained with the CNC machine, versus using a drill fixture for example.
CNC machining is used in several ways in our processes:
- To perform secondary operations such as roughing a pocket, drilling holes and adding a chamfer.
- To accurately make foam cast forms for Lost Foam Casting.
- To accurately make foam cast forms for rubber molding.
- To mill out solid dies for aluminum or urethane casting.
- To mill out templates and fixtures for custom products.
We have several CNC machines that are used in different ways. Out CNC router is primarily used to do light work, like foam, and wood cutting. Our larger Bridgeport mill has multi-tool capacity and is used for our heavier work on aluminum rims and our deap pocket urethane jobs, such as the Plumber Snake guide block.
To perform accurate CNC machining proper fixtures are required for production type orders. For example the wheels that we machine, require the hole center to be machined out, the face milled, and the holes drilled. Then the part has to be flipped to face the other side. This is all accomplished by holding the part accurately on the mill with a fixture. The fixture was developed using our 3D Modeling process and produced an accurate fixture from a casting developed in house.
A 3d print was developed initially to verify that the concept of fixturing was going to work with the rims that were being cast at the foundry. After the print was verified, aluminum shrink was added to the part and a pattern was developed. The pattern was coated with sodium silicated sand, and then the pattern pulled out of the hardened sand. The resultant cavity was then filled with aluminum and then allowed to cool.
The resulting fixture casting was sent to the machine shop to get the fill-face squared off and the main mounting holes drilled into it. The over-all diameter and shape did not require much if any changes to the diameter and mating faces.
Other customers we used 3D printed fixtures filled with urethane to hold the part on the CNC machine accurately. For example the Plumber-Snake-Machine Wear-Block was held in place using the 3d printed clamp fixture. The outside diameter of the part is clamped down circumferentially while the height of the part is stopped up against the internal structure on the CNC fixture.
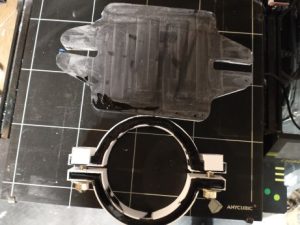
Fixtures are filled with urethane for strength
The Clamp was developed again using our 3D modeling process where the part was pre-fitted in the model and then 3d printed the fixture to verify the fit was going to work. After the test fit, the 3d print was altered so that it could be back filled with urethane. This makes the part very durable and allows it to have bending strength. This resulting fixture was then placed in the CNC machine and the located like conventional fixtures.
The part itself is clamped in place using a 3d printed circular clamp. It too is filled with urethane to make it flexible yet strong like a high strength plastic (i.e. UHMWPE or Nylon)