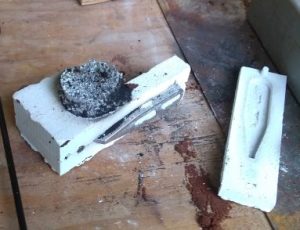
Plaster cast part out of aluminum. Surface finish is excellent.
Plaster is a material made out gypsum that hardens when water is dried out of it. The plaster material comes in powder form and requires precise mixtures of water with it to make the optimum slurry that can be then poured in molds. It has minimal shrinkage rates and will harden to chalky consistency.
It is ideal for making molds because it takes the form of the mold and maintains a precise shape when dried. Also, the material has extreme heat resistance and is unaffected by temperature when molten materials such as aluminum, brass and even cast iron are poured into them.
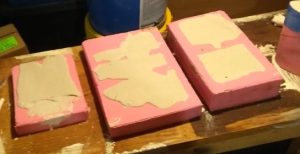
Plaster poured into face molds
In our process the same molds that are used for our sand molds can be used to make plaster casts, or molds.
Care must be taken when clamping the molds, however, as they are much more brittle when compared to our simple sand molds. The surface quality is extremely good and is primarily used for superior surface quality when it is needed.
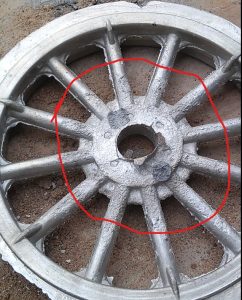
Steam sputtering in the center of the part. This is due to the molds not being dried out over a period of days. This mold only had 12 hours of drying time in a kiln.
The downside to plaster is that is requires extensive heat drying to be usable. If any moisture is left in the plaster the mold can explode, but more importantly will leave a steam skin deformation on the surface making the part rendered useless. Care must also be taken to make sure the mold has proper venting otherwise air bubbles will form on the surface of the part.
Additionally care must be taken to not allow too much air to be entrapped in the mix as the air bubbles can transmit their shape onto the surface of the part, leaving small bubble marks on a desired smooth surface.
The resultant part finish is done correctly is excellent. The part will not have sand voids and will require minimal clean up operations. It is ideal for parts that require clean surface finish.