Roto Molding is a method of casting where the mold itself is rotating in 3 directions. That might sound like a bit much, but the idea is to pin the liquid material (that is gradually hardening) to the walls of the mold. The best way to do this is to let gravity pull the material to face of the mold, however to get the face of the mold to get coated everywhere, the mold has to rotate essentially everywhere.
You may have watch the movie “The Great Stuff” or watched Ryan Gosling try to overcome the Gimbal machine while performing the hero Neil Armstrong (“First Man”). The guy Neil Armstrong, the first man to put his foot on the moon, that Neil Armstrong.
The Gimbal machine is essentially a chair that rotates in ALL directions. It can rotate clockwize and endwize while rotating all the axis together.
I probably lost you so I will say it a different way. If you roll your pencil on the table along its axis that is one direction. Then roll the pencil (though impossible to roll, more like flip) the pencil end over end (yeah flip.) Now roll the table. That is a gimbal.
It sounds complicated, but when put into practice it actually is not too bad. I’ve built my own roto-molder that actually works better than the professional roto-molder that I bought.
The molds are made usually out of two parts, with a distinct parting line. One half of the mold is partially filled with material and then the other mold half is quickly assembled and then clamped in place.
The machine is then turned on to tumble the closed mold for about 15 minutes. After that the part is de-molded and the next cycle begins.
The parts can range from small to large. Typically our clients parts are long and slender, but hollow. A thickness of .08 to .100 is achievable.
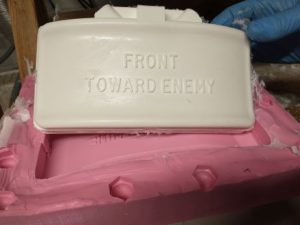
Our client sells props for movies. You may notice this “claymore mine” from several action films. The part is hollow.
The advantage of having hollow parts is that the parts are light weight but strong. Additionally, the parts are not one solid mass of urethane, which would be impractical.
The disadvantage of roto-molding is the time element. Only 4 parts per hour can be achieved. Additionally, even if more machines were gathered together the amount of man hours to man these machines is unchanged. The cost per hour is more expensive than conventional urethane casting, however many clients prefer the part quality and durability over the higher cost.
As with all urethane casting typically the tooling only lasts around 75 parts, so tooling costs need to be taken into account when utilizing this manufacturing method.